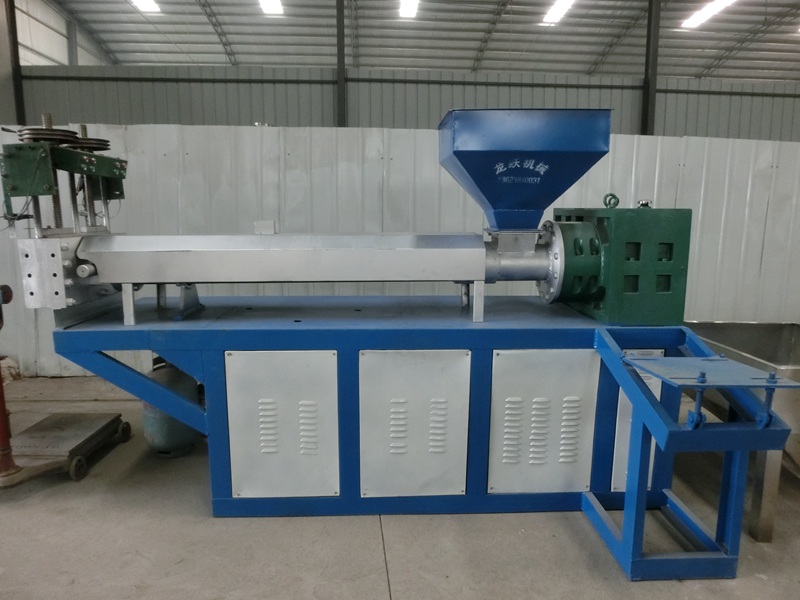
Working Principle Of Waste Plastic Granulator
The waste plastic granulator is composed of an extrusion system and a transmission system.
Screw: It is the most important part of the extruder. It is directly related to the application range and productivity of the extruder. It is made of high-strength, corrosion-resistant alloy steel.
Cylinder: It is a metal cylinder, generally made of alloy steel or composite steel pipe lined with alloy steel that is heat-resistant, high-pressure-resistant, strong, wear-resistant, and corrosion-resistant. The barrel and the screw are matched to realize the crushing, softening, melting, plasticizing, exhaust and compaction of the plastic, and the continuous and uniform delivery of the rubber material to the molding system. Generally, the length of the barrel is 15-30 times its diameter, so that the plastic can be fully heated and plasticized as a principle. It is also suitable for dry extrusion granulation. Although the wet granulation and dry granulation of the single-screw extrusion granulator are both extrusion methods, the scope of application of the two materials and the specific structural parameters of the screw machine itself are very different. 2.3 Compression ratio. The single screw of a single screw extruder is generally divided into two sections, the latter section (near the feed port) is the conveying section, and its function is to send the material forward; the former section (near the discharge I: 1) is the compression section, Its function is to compact the material and extrude the template to shape the material. Since the functions of the two sections of screws are different, their pitches are also different. The pitch of the conveying section is relatively fixed, generally 0.8 times the diameter of the screw, and the pitch of the compression section varies greatly with the material.
Hopper: The bottom of the hopper is equipped with a cut-off device to adjust and cut off the material flow. The side of the hopper is equipped with a sight hole and a calibration metering device.
Machine head and mold: The machine head is composed of an alloy steel inner sleeve and a carbon steel outer sleeve, and a forming mold is installed in the machine head. The function of the machine head is to transform the rotating plastic melt into parallel linear motion, uniformly and smoothly introduce it into the mold sleeve, and give the plastic the necessary molding pressure. The plastic is plasticized and compacted in the barrel, and flows into the molding die of the die through the neck of the die through the porous filter plate along a certain flow path. The die core and die sleeve are properly matched to form an annular gap with a decreasing cross-section, so that the plastic melt is in A continuous and dense tubular coating is formed around the core wire. In order to ensure that the plastic flow path in the die is reasonable and eliminate the dead angle of the accumulated plastic, a shunt sleeve is often installed. In order to eliminate pressure fluctuations during plastic extrusion, a pressure equalizing ring is also installed. The machine head is also equipped with a mold correction and adjustment device, which is convenient to adjust and correct the concentricity of the mold core and the mold sleeve. Since childhood, the teacher has always taught us to protect the environment, and we always say that protecting the environment is everyone’s responsibility, but what is the purpose of protecting the environment? When I was young, the cognition might be the garbage thrown on the ground. Pick it up and put it in the trash can. I help my mother sweep the floor at home, doing my own little effort. When I grow up, I don’t know how to protect the environment, but I see more plastic bags everywhere. , The cigarette butts in the corner of the street, the smelly garbage and waste water, the sky is not as blue as when it was small, all of this is caused by environmental pollution.
The waste plastic granulator consists of an extrusion system:
The extrusion system includes a hopper and a die. The plastic is plasticized into a uniform melt through the extrusion system, and the die is continuously extruded by the screw under the pressure established in the process.Screw: It is the most important part of the extruder. It is directly related to the application range and productivity of the extruder. It is made of high-strength, corrosion-resistant alloy steel.
Cylinder: It is a metal cylinder, generally made of alloy steel or composite steel pipe lined with alloy steel that is heat-resistant, high-pressure-resistant, strong, wear-resistant, and corrosion-resistant. The barrel and the screw are matched to realize the crushing, softening, melting, plasticizing, exhaust and compaction of the plastic, and the continuous and uniform delivery of the rubber material to the molding system. Generally, the length of the barrel is 15-30 times its diameter, so that the plastic can be fully heated and plasticized as a principle. It is also suitable for dry extrusion granulation. Although the wet granulation and dry granulation of the single-screw extrusion granulator are both extrusion methods, the scope of application of the two materials and the specific structural parameters of the screw machine itself are very different. 2.3 Compression ratio. The single screw of a single screw extruder is generally divided into two sections, the latter section (near the feed port) is the conveying section, and its function is to send the material forward; the former section (near the discharge I: 1) is the compression section, Its function is to compact the material and extrude the template to shape the material. Since the functions of the two sections of screws are different, their pitches are also different. The pitch of the conveying section is relatively fixed, generally 0.8 times the diameter of the screw, and the pitch of the compression section varies greatly with the material.
Hopper: The bottom of the hopper is equipped with a cut-off device to adjust and cut off the material flow. The side of the hopper is equipped with a sight hole and a calibration metering device.
Machine head and mold: The machine head is composed of an alloy steel inner sleeve and a carbon steel outer sleeve, and a forming mold is installed in the machine head. The function of the machine head is to transform the rotating plastic melt into parallel linear motion, uniformly and smoothly introduce it into the mold sleeve, and give the plastic the necessary molding pressure. The plastic is plasticized and compacted in the barrel, and flows into the molding die of the die through the neck of the die through the porous filter plate along a certain flow path. The die core and die sleeve are properly matched to form an annular gap with a decreasing cross-section, so that the plastic melt is in A continuous and dense tubular coating is formed around the core wire. In order to ensure that the plastic flow path in the die is reasonable and eliminate the dead angle of the accumulated plastic, a shunt sleeve is often installed. In order to eliminate pressure fluctuations during plastic extrusion, a pressure equalizing ring is also installed. The machine head is also equipped with a mold correction and adjustment device, which is convenient to adjust and correct the concentricity of the mold core and the mold sleeve. Since childhood, the teacher has always taught us to protect the environment, and we always say that protecting the environment is everyone’s responsibility, but what is the purpose of protecting the environment? When I was young, the cognition might be the garbage thrown on the ground. Pick it up and put it in the trash can. I help my mother sweep the floor at home, doing my own little effort. When I grow up, I don’t know how to protect the environment, but I see more plastic bags everywhere. , The cigarette butts in the corner of the street, the smelly garbage and waste water, the sky is not as blue as when it was small, all of this is caused by environmental pollution.