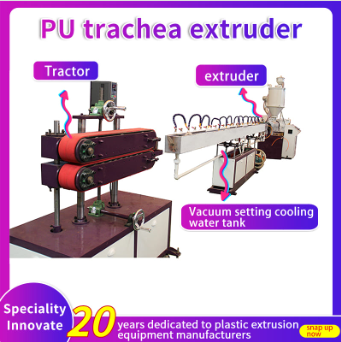
Unlock Efficient Production: The Ultimate Guide to Tube Extruders
In the realm of manufacturing, efficiency and precision are paramount for achieving high-quality products while minimizing costs. One crucial tool in this endeavor is the tube extruder, a device that shapes raw materials into continuous tubes used across various industries, from medical devices to aerospace components. This guide delves into the world of tube extruders, exploring their applications, technologies, and best practices for optimizing production.
Introduction to Tube Extrusion
Tube extrusion is a manufacturing process that involves forcing molten materials through a die to create hollow tubes. This process is versatile, allowing for the production of tubes with precise dimensions and properties tailored to specific applications. The extrusion process begins with selecting the appropriate raw material, such as plastics like PVC, PE, or PP, which are then melted and pushed through a die to form the desired tube shape.
Applications of Tube Extruders
Medical Applications
In the medical field, tube extruders play a vital role in producing critical components for devices such as stents, catheters, and drug delivery systems. The precision and customizability of extruded tubing enable the creation of tubes with specific diameters, wall thicknesses, and properties essential for medical applications. For instance, variable flexibility can be achieved by adjusting the material blend and extrusion parameters, making it ideal for catheters that require both rigidity and maneuverability.
Multilumen Tubes: One of the significant advancements in medical tubing is the development of multilumen tubes. These tubes have multiple channels, each capable of performing different functions, such as medication delivery while monitoring body functions. The use of biocompatible and bioresorbable materials further enhances the safety and efficacy of these medical devices, eliminating the need for surgical removal after they have served their purpose.
Aerospace Applications
In aerospace, tube extruders are used to produce high-strength, lightweight tubing essential for fluid transport systems and structural components. The extrusion process allows for the creation of tubes with precise tolerances and high strength-to-weight ratios, which are critical in aerospace applications where materials must withstand extreme temperatures and pressures.
Technologies and Innovations in Tube Extrusion
Advanced Materials
Recent advancements in polymer technology have led to the development of high-performance materials such as thermoplastic elastomers (TPEs), polyether ether ketone (PEEK), and bioresorbable materials. These materials offer improved biocompatibility and mechanical properties, making them ideal for medical and aerospace applications.
Multi-Layer Extrusion Systems
Multi-layer extrusion systems are increasingly used in medical tubing to create tubes with multiple layers, each offering distinct advantages. For example, the outer layer can provide abrasion resistance, while the innermost layer ensures biocompatibility. This multi-layer design enhances the tube's strength, flexibility, and functionality, allowing for personalized properties such as drug delivery systems.
Precision Extrusion Technologies
Precision extrusion relies on advanced technologies like computer numerical control (CNC) and in-line measurement systems to ensure exact control over material shape and dimensions. CNC systems enable the creation of custom tooling for complex tubing with tight tolerances, while in-line measurement systems monitor and control tube dimensions during production.
Best Practices for Optimizing Tube Extrusion
Raw Material Selection
Optimizing raw material selection is crucial for cost-effectiveness and product quality. This involves choosing materials that meet application requirements while considering factors like cost, durability, and environmental impact. Blending virgin and recycled materials can also enhance cost-effectiveness without compromising product quality.
Process Parameter Adjustment
Adjusting extrusion equipment settings to suit the selected raw materials is essential for optimal processing performance. Parameters such as temperature, pressure, and screw design must be carefully adjusted to prevent issues like thermal degradation and inconsistent thickness.
Quality Control
Implementing robust quality control measures is vital to ensure that extruded tubes meet specifications. This includes monitoring the extrusion process in real-time using technologies like laser gauges and micrometers to maintain precise dimensions and surface finish.
Conclusion
Tube extruders are indispensable tools in modern manufacturing, offering precision and versatility across various industries. By understanding the applications, technologies, and best practices associated with tube extrusion, manufacturers can unlock efficient production processes that meet the demands of today's complex and evolving markets. As technology continues to advance, the future of tube extrusion holds promise for even greater precision, sustainability, and innovation.