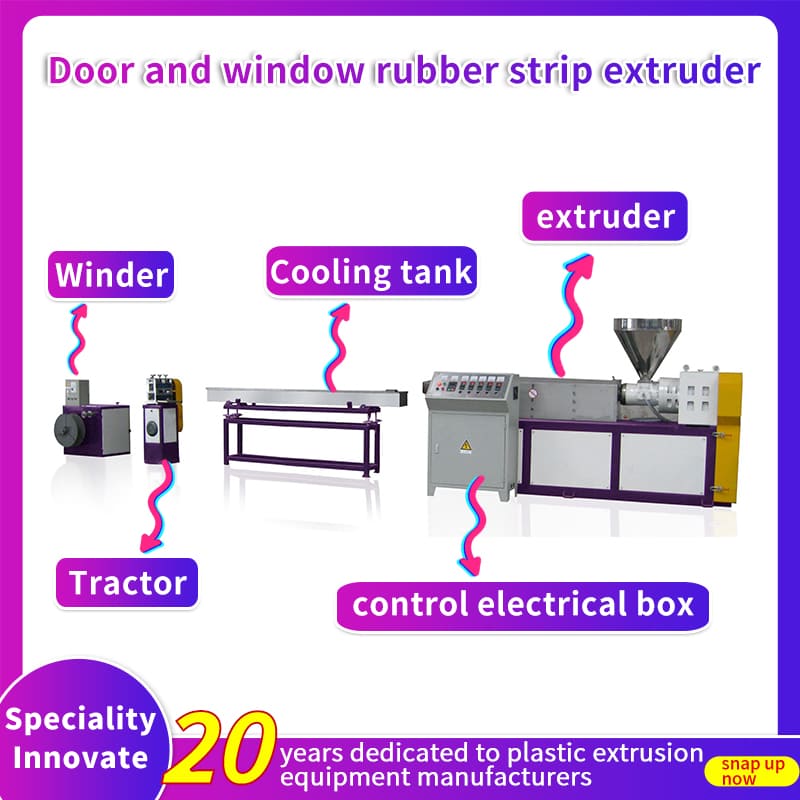
The Ultimate Guide to Window and Door Seal Strip Extruders
Window and door seal strips are essential components in modern construction, providing insulation, weatherproofing, and energy efficiency to buildings. The manufacturing of these seal strips involves a sophisticated process known as extrusion, which requires specialized machinery called extruders. In this comprehensive guide, we will delve into the world of window and door seal strip extruders, exploring their role, the extrusion process, the types of materials used, and the benefits they offer.
Introduction to Extruders
Extruders are machines designed to shape and form materials, such as rubber, plastics, and other polymers, into continuous profiles. These profiles can be customized to fit various applications, including window and door seals. The extrusion process involves heating the raw material until it becomes pliable, then forcing it through a die to create the desired shape. This process allows for the mass production of uniform seal strips with precise dimensions and properties.
The Extrusion Process
The extrusion process for window and door seal strips involves several key steps:
Material Selection and Preparation: The first step is to select the appropriate material for the seal strip. Common materials include rubber (such as EPDM and silicone), PVC, and TPE. These materials are chosen based on their durability, resistance to weathering, and ability to provide a tight seal.
Feeding the Material: The selected material is then fed into the extruder. For solid materials like rubber, a strip feeder is typically used, while softer compounds might require a cold feeder.
Heating and Mixing: Inside the extruder, the material is heated and mixed by a rotating screw. This process ensures uniform temperature and pressure distribution, making the material pliable and ready for shaping.
Shaping the Profile: The heated material is then forced through a die, which gives it the desired shape. The die is specifically designed to produce the precise cross-sectional profile required for window and door seals.
Cooling and Cutting: After extrusion, the profile is cooled in a cooling chamber to solidify it. Finally, it is cut to the required length using a cutting machine.
Types of Extruders
There are several types of extruders used in the production of window and door seal strips, each suited to different materials and applications:
Single-Screw Extruders: These are the most common type and are suitable for most thermoplastic materials. They offer simplicity and cost-effectiveness but may have limitations in terms of material mixing and heat transfer.
Twin-Screw Extruders: These extruders provide better mixing and heat transfer, making them ideal for more complex materials or coextrusion processes. They are more versatile but also more expensive.
Coextruders: These machines allow for the simultaneous extrusion of multiple materials, creating multi-layered seal strips. This is useful for producing seals with different properties in different layers, such as a sponge rubber core with a harder outer layer.
Materials Used for Seal Strips
The choice of material for window and door seal strips depends on the desired properties and application:
EPDM (Ethylene Propylene Diene Monomer): Known for its excellent weather resistance, EPDM is widely used for outdoor applications. It offers good UV resistance and can withstand extreme temperatures.
Silicone Rubber: Offers excellent flexibility and resistance to extreme temperatures. It is often used in high-performance applications where durability is crucial.
PVC (Polyvinyl Chloride): PVC is cost-effective and easy to process. It is commonly used for PVC strips but may not offer the same level of weather resistance as rubber materials.
TPE (Thermoplastic Elastomer): Combines the benefits of rubber and plastics, offering flexibility and ease of processing. TPE is used in applications where a balance between performance and cost is needed.
Benefits of Seal Strips
Window and door seal strips provide several benefits to buildings:
Energy Efficiency: By sealing gaps around doors and windows, these strips help reduce heat loss in winter and heat gain in summer, thereby improving energy efficiency.
Weatherproofing: They protect buildings from rain, wind, and other environmental factors, extending the lifespan of doors and windows.
Noise Reduction: Seal strips can also act as sound barriers, reducing noise pollution and improving indoor comfort.
Durability: High-quality seal strips are designed to withstand the elements and last for many years, reducing maintenance costs.
Applications of Seal Strips
Seal strips are used in a wide range of applications:
Residential Buildings: Essential for maintaining a comfortable indoor climate and reducing energy bills.
Commercial Buildings: Helps in maintaining structural integrity and improving energy efficiency.
Industrial Facilities: Used in machinery and equipment to prevent dust and moisture ingress.
Automotive Industry: Used for sealing doors, windows, and other components.
Conclusion
Window and door seal strip extruders are critical in producing high-quality seal strips that meet the demands of modern construction. By understanding the extrusion process, the types of materials used, and the benefits these seal strips offer, manufacturers can optimize their production to meet growing market demands. As the world moves towards more sustainable and energy-efficient buildings, the role of window and door seal strips will become increasingly important, driving innovation and growth in the extrusion industry.