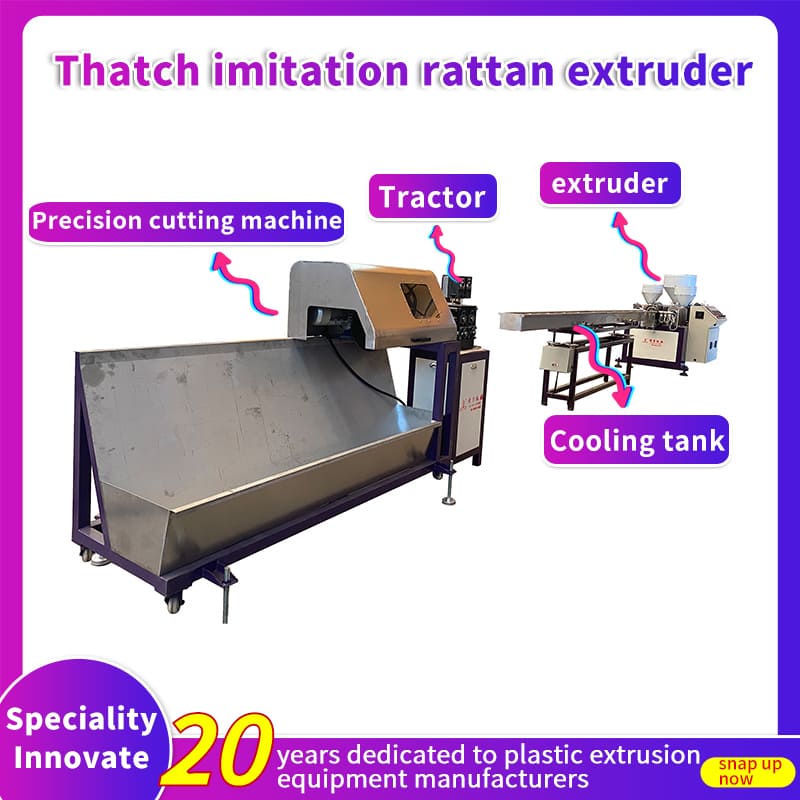
The Ultimate Guide to Rattan Imitation Extrusion Machines
Synthetic rattan has revolutionized the furniture, decor, and handicraft industries due to its durability, versatility, and aesthetic appeal. Rattan imitation extrusion machines are at the heart of this revolution, enabling manufacturers to produce high-quality synthetic rattan efficiently and consistently. This guide provides a comprehensive overview of rattan imitation extrusion machines, covering their types, key components, benefits, applications, and maintenance tips.
What is a Rattan Imitation Extrusion Machine?
A rattan imitation extrusion machine is a specialized piece of equipment designed to produce synthetic rattan strands. The process involves melting polymer materials such as polyethylene (PE), polypropylene (PP), or polyvinyl chloride (PVC), and then forcing them through a die to create rattan-like strips. These strips are then used to manufacture various products, including furniture, baskets, and decorative items. These machines can produce single- or multi-color rattan, with different shapes and textures achieved through different extrusion molds.
Types of Rattan Extrusion Machines
Rattan extrusion machines come in several types, each designed for specific production needs. The primary classifications are based on the extrusion process, the materials used, and the final product characteristics.
PE Rattan Extrusion Machine: This type uses PE as the primary raw material. The extruder mixes the raw materials, such as powdered calcium carbonate and fiber, and sends them to the heating barrel. The high temperature and pressure change the materials into a viscous liquid, which is then pumped and formed into strands through a die plate.
Coextrusion Rattan Extrusion Machine: These machines produce multi-layered rattan with a soft outer layer and a high-strength core. This design enhances the product's longevity, resistance, and aesthetic appeal.
Multi-Color Rattan Extrusion Machine: These machines create colored rattan for decorative items like lampshades, flowerpots, and baskets. The colored rattan can also substitute natural bamboo for indoor and outdoor decoration.
Straight Line Rattan Extrusion Machine: These machines produce straight artificial rattan strands, typically used in weaving to create smooth and even wicker. The straight-line profile allows for uniform spacing and consistent quality.
Curved Rattan Extrusion Machine: These are suited for producing curved lines or arcs, offering versatility in creating intricate and artistic designs for architectural decoration, leisure facilities, and landscape ornaments.
Key Components of a Rattan Extrusion Machine
A typical rattan extrusion machine comprises several essential components that work together to ensure efficient and high-quality production.
Extruder: The core of the machine, responsible for melting and mixing the plastic material. It consists of a screw and barrel system where the plastic is heated, compressed, and pushed towards the die.
Screw and Barrel: The screw rotates inside the barrel, conveying the plastic material through different heating zones. The design of the screw is crucial for effective mixing and consistent material flow.
Die: This is a specially designed tool that shapes the molten plastic into the desired rattan profile. Different dies can be used to produce various shapes, including round, flat, and embossed rattan.
Heating System: This system consists of heaters that precisely control the temperature of the barrel to ensure the plastic melts evenly. Accurate temperature control is essential for maintaining the quality of the extruded rattan.
Cooling System: After extrusion, the rattan strands pass through a cooling bath or cooling system to solidify and maintain their shape. This system typically uses water or air to rapidly cool the plastic.
Traction or Haul-off Unit: This unit pulls the cooled rattan strands from the die at a constant speed, ensuring consistent dimensions and preventing deformation
Winding Machine: The winding machine collects the finished rattan strands onto spools or reels for easy handling and storage.
Control System: Modern machines feature user-friendly interfaces with automated settings and real-time monitoring. These systems allow operators to control temperature, speed, and other parameters, ensuring optimal production.
Benefits of Using Rattan Extrusion Machines
Investing in a rattan extrusion machine offers numerous advantages for manufacturers.
Enhanced Production Efficiency: These machines streamline the production process, enabling faster manufacturing cycles and higher output volumes.
Consistent Quality: Precise extrusion mechanisms ensure the uniformity and durability of synthetic rattan strands, crucial for producing high-quality finished products.
Cost Savings: By automating key production steps and reducing material waste, rattan extrusion machines can significantly lower overall manufacturing costs.
Customization Options: Manufacturers can easily adapt production to meet specific client requirements, such as color, thickness, and texture.
Environmental Sustainability: Many machines are designed to minimize material waste and energy consumption, contributing to more sustainable manufacturing practices.
Applications of Synthetic Rattan
Synthetic rattan produced by extrusion machines is used across various industries.
Furniture Manufacturing: It is used for crafting durable and weather-resistant chairs, tables, and sofas.
Decorative Items: This includes baskets, mats, and other woven products for homes and offices.
Outdoor Structures: Synthetic rattan is commonly used for fencing and gazebos due to its ability to withstand harsh weather conditions.
Automotive Industry: Some car interiors feature synthetic rattan components for unique aesthetics.
Maintenance Tips for Rattan Extrusion Machines
Proper maintenance is essential for ensuring the longevity and efficient operation of rattan extrusion machines. Regular maintenance can prevent costly repairs and downtime.
Regular Cleaning: Clean the machine regularly to remove any plastic residue or debris. Pay special attention to the screw, barrel, and die.
Lubrication: Lubricate moving parts such as screws, rollers, and bearings to prevent wear and ensure smooth operation.
Temperature Control: Regularly check and calibrate temperature sensors and heaters to ensure accurate and consistent heating.
Cooling System Maintenance: Ensure the cooling system is clean and functioning correctly to maintain the quality of the extruded rattan.
Inspection of Electrical Components: Regularly inspect electrical components for wear or damage. Replace any faulty components promptly.
Screw and Barrel Maintenance: Periodically inspect the screw and barrel for wear and scratches. Clean the screw and barrel with oil to prevent rust and corrosion.
Gearbox Maintenance: Change the gearbox oil every 4000 to 5000 hours of operation, or at least once a year.
Hydraulic System Maintenance: Replace the oil filter element of the hydraulic system every six months and regularly check the pressure of the energy storage tank.
Common Problems and Solutions
Like any machinery, rattan extrusion machines can experience faults. Understanding these common issues and their solutions can help maintain efficient operations and minimize downtime.
Main Motor Fails to Start: This can be due to electrical issues, insufficient heating time, or mechanical problems. Check the power supply, heaters, and motor components.
Unstable Main Motor Current: Uneven feeding, damaged motor bearings, or faulty heaters can cause this. Troubleshoot the feeding machine, inspect the motor bearings, and verify that all heaters function correctly.
Obstructed Material Discharge from the Die: This can be caused by inoperative heaters, low operating temperatures, or foreign objects in the system. Confirm that all heaters are functioning properly, adjust the operating temperature, and thoroughly clean the extrusion system.
Abnormal Noise from the Main Motor: Damaged motor bearings or a faulty silicon rectifier in the motor control circuit can cause this. Replace the motor bearings if they are damaged and inspect the silicon rectifier components.
Conclusion
Rattan imitation extrusion machines are essential for producing high-quality synthetic rattan products efficiently and sustainably. These machines offer numerous benefits, from consistent quality and customization to cost savings and environmental sustainability. By understanding the different types of machines, their key components, and proper maintenance practices, manufacturers can optimize their production processes and meet the growing demand for synthetic rattan products. Regular maintenance, prompt troubleshooting, and investing in high-quality machinery are key to maximizing the benefits of rattan extrusion technology.