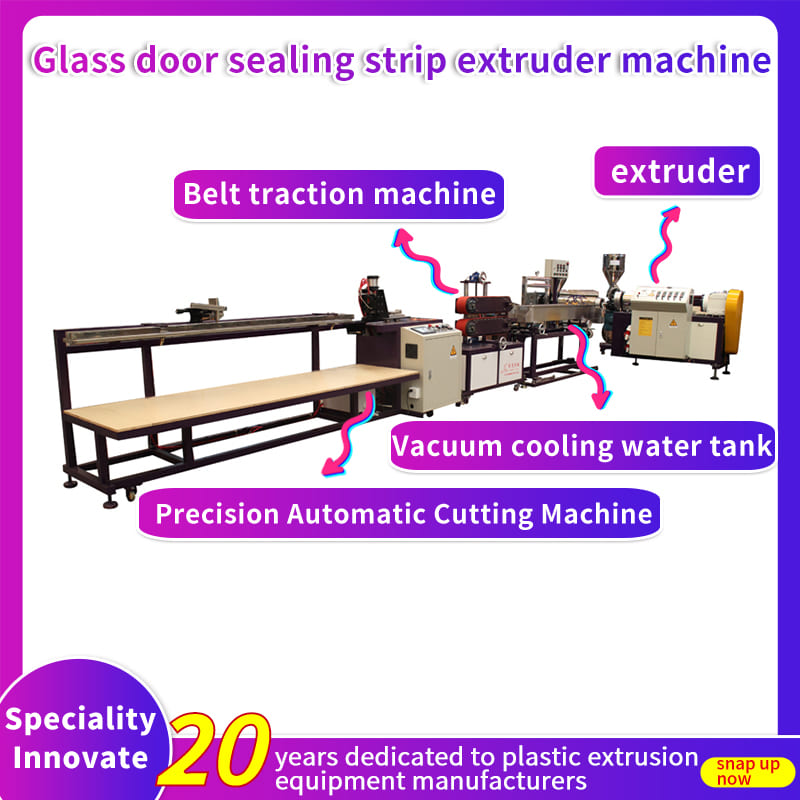
The Role of Glass Door Seal Strip Extruders in Modern Manufacturing
In the realm of modern manufacturing, precision and efficiency are paramount. One critical component that plays a significant role in ensuring the integrity and functionality of various products, particularly in the construction and automotive sectors, is the seal strip. Glass door seal strip extruders are specialized machines designed to produce these essential components, which are crucial for maintaining the structural integrity and energy efficiency of doors and windows. This article delves into the importance, functionality, and benefits of glass door seal strip extruders in contemporary manufacturing processes.
Introduction to Seal Strips
Seal strips, often made from materials like PVC, rubber, or silicone, are used to create a tight seal between two surfaces, such as doors and their frames. They are essential for preventing air leaks, water ingress, and noise penetration. These strips are particularly important in the context of glass doors as they help maintain the door's insulation properties and prevent moisture from entering the gap between the door and its frame.
The Functionality of Glass Door Seal Strip Extruders
Glass door seal strip extruders are sophisticated machines that utilize the extrusion process to manufacture seal strips. The extrusion process involves feeding raw materials, such as PVC pellets or rubber compounds, into a heated barrel where they are melted and mixed. The molten material is then forced through a die, which shapes it into the desired profile. This process allows for the production of seal strips with precise dimensions and consistent quality, which is crucial for ensuring a tight seal.
Key Components of a Glass Door Seal Strip Extruder
Heated Barrel: This is where the raw material is melted and mixed. The temperature and pressure in this section are critical for achieving the right consistency and flow of the material.
Screw and Barrel Assembly: The screw inside the barrel mixes and pushes the molten material towards the die. The design of the screw and barrel assembly affects the efficiency and quality of the extrusion process.
Die: The die determines the shape and size of the seal strip. It is designed to produce strips with specific cross-sectional profiles that match the requirements of different applications.
Cooling System: After extrusion, the strip is cooled to solidify it. This step is crucial for maintaining the strip's shape and ensuring it meets the required specifications.
Cutting and Finishing: The final step involves cutting the extruded strip to the desired length and applying any additional finishes, such as coatings or adhesives.
Benefits of Using Glass Door Seal Strip Extruders
The use of glass door seal strip extruders offers several benefits that make them indispensable in modern manufacturing:
1. Enhanced Durability
Material Resistance: PVC and rubber seal strips produced by these extruders are resistant to weathering, chemical degradation, and UV exposure, making them ideal for outdoor applications.
Consistent Quality: The precision of the extrusion process ensures that the seal strips are consistent in quality, reducing the likelihood of defects and improving overall durability.
2. Improved Performance and Functionality
Customization: Extruders can produce seal strips in various shapes and sizes, allowing manufacturers to tailor their products to specific applications. For example, thicker strips might be used for heavy-duty doors, while thinner strips could be used for lighter applications.
Sealing Integrity: The precise dimensions of the extruded strips ensure a perfect fit, which is essential for maintaining sealing integrity and preventing leaks or drafts.
3. Cost-Effectiveness and Efficiency
Automation: The automated nature of extrusion machines reduces labor costs and increases production speed, allowing manufacturers to produce large volumes of seal strips quickly.
Material Optimization: Manufacturers can choose the most cost-effective raw materials without compromising on quality, thanks to the flexibility of extrusion machines to work with multiple formulations.
4. Flexibility in Application
Multi-Industry Use: Glass door seal strip extruders are not limited to producing seals for glass doors alone. They can be adapted to manufacture seals for various applications across multiple industries, including automotive, construction, and consumer goods.
Customization for Different Environments: Depending on the intended use, manufacturers can adjust the formulation of the material and the extrusion process to produce seal strips that meet specific environmental demands, such as high-temperature resistance or chemical resistance.
5. Environmental Sustainability
Efficiency and Waste Reduction: The precision of the extrusion process minimizes material waste, contributing to a more sustainable production process.
Energy Efficiency: Modern extruders are designed to consume less energy, further reducing the environmental impact of seal strip production.
Conclusion
Glass door seal strip extruders play a vital role in modern manufacturing by providing a cost-effective and efficient means of producing high-quality seal strips. These machines are essential for ensuring the durability and performance of doors and windows, contributing to energy efficiency and structural integrity. As technology continues to evolve, the importance of these extruders will only grow, enabling manufacturers to meet the increasingly stringent demands of various industries while maintaining sustainability and efficiency.
In summary, the role of glass door seal strip extruders in modern manufacturing is multifaceted, offering benefits that range from enhanced durability and improved performance to cost-effectiveness and environmental sustainability. As industries continue to evolve, the demand for these specialized machines will remain strong, driving innovation and efficiency in the production of seal strips for a wide range of applications.