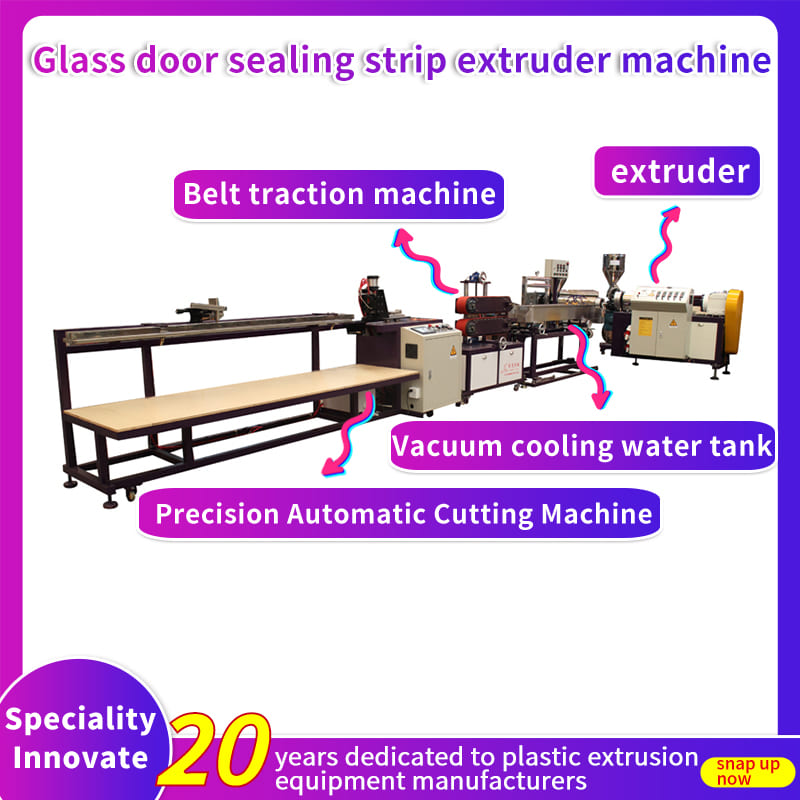
A Comprehensive Guide to Plastic Strip Extruders
Plastic strip extruders are essential machines in the manufacturing of various plastic products, allowing for the efficient production of items with consistent cross-sectional profiles. This comprehensive guide explores the workings of plastic strip extruders, their components, advantages, applications across industries, and the future of this technology.
Understanding Plastic Strip Extrusion
Plastic extrusion is a process that transforms raw plastic materials into continuous lengths of products with a defined shape. The process is widely utilized due to its efficiency and versatility. It begins with plastic granules being fed into a hopper, where they are melted and shaped into the desired form through a die.
The Extrusion Process
The extrusion process consists of several key stages:
Feeding: Plastic pellets are introduced into the hopper.
Melting: As the pellets move through a heated barrel, they are melted by heat generated from both external heaters and mechanical friction created by a rotating screw.
Shaping: The molten plastic is forced through a die that shapes it into a continuous profile.
Cooling: After exiting the die, the extruded product is cooled to solidify it before being cut or rolled.
This continuous process allows manufacturers to produce large quantities of plastic strips efficiently.
Key Components of Plastic Strip Extruders
Understanding the components of plastic strip extruders is crucial for grasping how they function:
Hopper: The entry point for raw plastic materials.
Feed Throat: Transfers materials from the hopper to the barrel.
Breaker Plate: Maintains pressure within the barrel and filters out impurities.
Barrel: Heats and melts the plastic while conveying it forward via a rotating screw.
Die: Determines the shape of the extruded product.
Cooling System: Rapidly cools the extruded material to solidify it.
These components work together seamlessly to ensure efficient production.
Advantages of Plastic Strip Extruders
Plastic strip extruders offer numerous benefits that make them a preferred choice in manufacturing:
High Efficiency: The continuous nature of extrusion allows for high-speed production, making it suitable for large-scale manufacturing.
Cost-Effectiveness: Lower operational costs arise from reduced labor needs and minimal waste generation. The ability to reuse scrap material further enhances cost savings.
Versatility: They can handle various types of thermoplastics, including polyethylene (PE), polypropylene (PP), and polyvinyl chloride (PVC), making them suitable for diverse applications.
Customizability: Manufacturers can easily modify extrusion parameters to create custom profiles tailored to specific needs, including variations in thickness, hardness, and color.
Consistency and Quality: The process ensures uniformity in product dimensions and properties, which is vital for applications requiring precise specifications.
Applications Across Industries
The versatility of plastic strip extruders allows them to serve multiple industries effectively. Here are some key sectors where they play a crucial role:
1. Automotive Industry
In automotive manufacturing, plastic strip extruders produce components such as weather seals, gaskets, and interior trim pieces. These parts benefit from lightweight yet durable materials that improve fuel efficiency and reduce vehicle weight. Additionally, their resistance to chemicals and UV exposure enhances durability in harsh environments.
2. Construction
Plastic strips are widely used in construction for window frames, door seals, siding, and roofing components. Their moisture resistance and thermal efficiency contribute to energy-efficient building practices. Moreover, their lightweight nature simplifies installation processes.
3. Packaging
The packaging industry utilizes plastic strip extrusion to create films, sheets, and containers that protect products while extending shelf life. Customizable barrier properties allow manufacturers to tailor packaging solutions for different products.
4. Medical Applications
In healthcare settings, extruded plastics are essential for producing medical tubing, catheters, and other critical components. The ability to use medical-grade materials ensures compliance with stringent regulatory requirements while providing the durability and flexibility necessary for medical devices.
5. Consumer Goods
Plastic strip extruders cater to consumer goods by producing items such as household appliances' handles, toys, and gardening tools. The adaptability of extruded plastics allows manufacturers to meet diverse consumer demands efficiently.
6. Electrical and Electronics
In this sector, plastic extrusions are employed for cable management systems and insulating profiles for wires. The excellent electrical insulation properties of certain thermoplastics make them suitable for these applications.
Innovations in Plastic Strip Extrusion Technology
The field of plastic strip extrusion is continually evolving with technological advancements aimed at improving efficiency and product quality:
Co-extrusion Technology: This method allows multiple layers of different materials to be extruded simultaneously through a single die, enabling enhanced functionalities such as barrier properties or aesthetic features.
Servo-driven Extruders: These machines provide precise control over the extrusion process while consuming less energy than traditional hydraulic systems, contributing to lower operational costs.
Integration of AI: Artificial intelligence helps optimize extrusion processes by analyzing data in real time to make adjustments that enhance efficiency and reduce waste.
Advanced Cooling Systems: New cooling technologies improve cooling rates and control during production, ensuring dimensional stability in extruded products.
Conclusion
Plastic strip extruders play a vital role in modern manufacturing across various industries due to their efficiency, versatility, and ability to produce high-quality products consistently.
Understanding the intricacies of this process not only highlights its importance but also showcases its potential for future growth across diverse sectors. Whether improving vehicle performance or enhancing medical device functionality, plastic strip extruders will remain at the forefront of industrial innovation as they adapt to meet changing market demands.