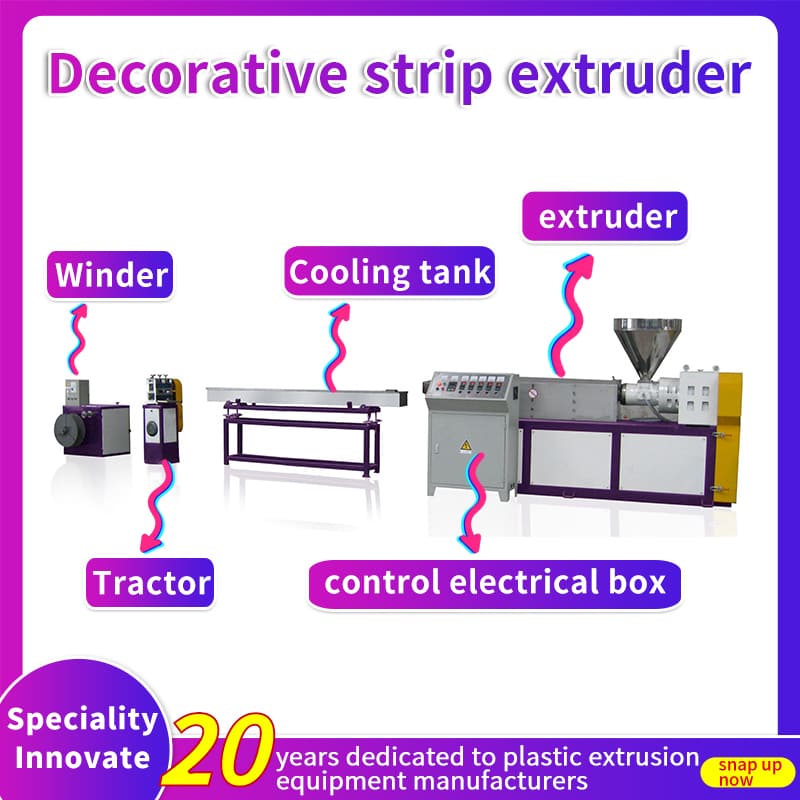
Plastic Strip Extruders Explained: Key Benefits and Applications Across Industries
Plastic strip extruders are pivotal in the manufacturing landscape, enabling the production of a wide array of plastic products across various industries. This article delves into the mechanics of plastic strip extrusion, its numerous benefits, and its applications in different sectors.
Understanding Plastic Strip Extrusion
Plastic extrusion is a high-volume manufacturing process that transforms raw plastic materials into continuous lengths of products with a fixed cross-sectional profile. The process begins with plastic granules being fed into an extruder hopper, where they are gradually melted by heat generated from rotating screws and heated barrels. The molten plastic is then forced through a die that shapes it into the desired profile, which can include strips, sheets, tubes, and more.
The Extrusion Process
Feeding: Raw plastic materials are loaded into the hopper.
Melting: The materials move through a heated barrel where they are melted and mixed. The temperature is carefully controlled to ensure proper melting without degradation.
Shaping: Once melted, the plastic is pushed through a die that determines its final shape.
Cooling: The extruded product is cooled to solidify it before being cut to length or rolled for storage.
This process allows for the creation of complex shapes and profiles that meet specific design requirements, making it highly versatile.
Key Benefits of Plastic Strip Extruders
Plastic strip extruders offer several advantages that contribute to their widespread use in manufacturing:
Versatility: They can produce a wide range of products, from simple strips to complex profiles used in various applications.
Cost-effectiveness: The extrusion process is efficient for high-volume production, reducing costs per unit significantly compared to other manufacturing methods.
Customizability: Manufacturers can create tailored profiles to meet specific customer needs, including variations in thickness, hardness, and color.
Consistency and Quality: The continuous nature of the extrusion process ensures uniformity in product dimensions and quality, which is crucial for applications requiring precise specifications.
Material Efficiency: Extrusion minimizes waste by utilizing almost all of the raw material, making it an environmentally friendly option compared to other methods that generate more scrap.
Applications Across Industries
The versatility of plastic strip extruders allows them to serve multiple industries effectively. Here are some key sectors where they play a crucial role:
1. Automotive Industry
In the automotive sector, plastic strip extruders are used to manufacture components such as weather seals, gaskets, and interior trim pieces. These parts benefit from the lightweight yet durable nature of extruded plastics, which helps improve fuel efficiency and reduce vehicle weight. Additionally, the resistance of these materials to chemicals and UV exposure enhances their longevity in harsh environments.
2. Construction
Plastic strips are widely used in construction for window frames, door seals, siding, and roofing components. Their resistance to moisture and thermal efficiency makes them ideal for energy-efficient building practices. Moreover, their lightweight nature simplifies installation processes.
3. Packaging
The packaging industry utilizes plastic strip extrusion to create films, sheets, and containers that protect products while extending shelf life. The ability to customize barrier properties allows manufacturers to tailor packaging solutions for different products.
4. Medical Applications
In healthcare, extruded plastics are essential for producing medical tubing, catheters, and other critical components. The ability to use medical-grade materials ensures compliance with stringent regulatory requirements while providing the durability and flexibility necessary for medical devices.
5. Consumer Goods
Plastic strip extruders also cater to consumer goods by producing items such as household appliances' handles, toys, and gardening tools. The adaptability of extruded plastics allows manufacturers to meet diverse consumer demands efficiently.
6. Electrical and Electronics
In this sector, plastic extrusions are employed for cable management systems, insulating profiles for wires, and housing for electronic devices. The excellent electrical insulation properties of certain thermoplastics make them suitable for these applications.
Conclusion
Plastic strip extruders are integral to modern manufacturing across various industries due to their versatility, cost-effectiveness, and ability to produce high-quality products consistently. As technology continues to advance in this field, we can expect further innovations that will enhance the capabilities of plastic extrusion processes. This ongoing evolution will likely lead to even broader applications and improved efficiencies in manufacturing practices globally.
In summary, understanding the mechanics behind plastic strip extrusion not only highlights its importance but also illustrates its potential for future growth across diverse sectors. Whether it's improving vehicle performance or enhancing medical device functionality, plastic strip extruders will remain at the forefront of industrial innovation.