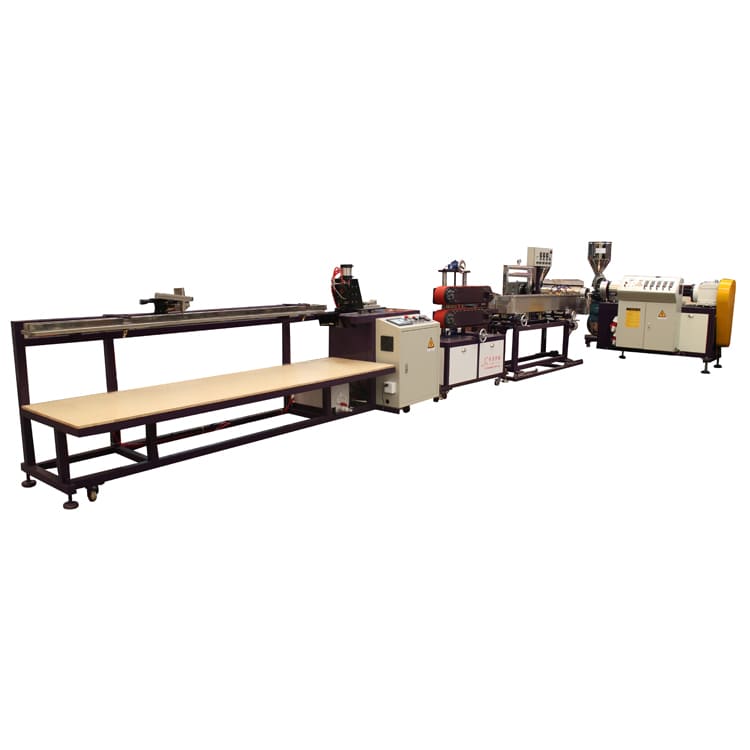
Innovations in Glass Door Seal Strip Extrusion: Enhancing Efficiency and Quality
The manufacturing industry has witnessed remarkable advancements over the past few decades, particularly in the production of sealing solutions like glass door seal strips. These innovations not only enhance efficiency and quality but also contribute significantly to energy conservation and structural integrity in various applications. This article explores the latest developments in glass door seal strip extrusion, emphasizing the technologies, processes, and benefits that come with these innovations.
Understanding Glass Door Seal Strips
Glass door seal strips are essential components used to create airtight and watertight seals around glass doors. These strips are typically made from materials such as PVC, rubber, or silicone, each chosen for its unique properties that contribute to durability and performance. The primary functions of these seal strips include:
Preventing Air Leaks: Ensuring energy efficiency by minimizing drafts.
Water Resistance: Protecting against moisture ingress, which can lead to structural damage.
Noise Reduction: Enhancing comfort by reducing sound transmission.
Given the critical role that seal strips play in maintaining the functionality of glass doors, the extrusion process used to manufacture them must be precise and efficient.
The Extrusion Process Explained
Extrusion is a manufacturing process where raw materials are melted and shaped into continuous profiles. In the context of glass door seal strip production, this involves several key steps:
Material Preparation: Raw materials, such as PVC pellets or rubber compounds, are fed into an extruder.
Melting and Mixing: The materials are heated in a barrel until they reach a molten state. A rotating screw within the barrel ensures thorough mixing.
Shaping: The molten material is forced through a die that shapes it into the desired profile of the seal strip.
Cooling: After exiting the die, the newly formed strip is cooled to solidify its shape.
Cutting and Finishing: Finally, the extruded strip is cut to length and may undergo additional finishing processes such as coating or adhesive application.
This streamlined process allows manufacturers to produce high volumes of seal strips with consistent quality and precision.
Innovations Driving Efficiency
Recent technological advancements have significantly improved the efficiency of glass door seal strip extrusion. Key innovations include:
Co-Extrusion Technology: This method combines two or more materials during the extrusion process, allowing for the creation of seal strips with varying properties. For example, a soft outer layer can provide better sealing performance while a harder inner layer offers structural support.
Automated Systems: Modern extrusion lines are increasingly automated, reducing labor costs and minimizing human error. Automation also enhances production speed, allowing manufacturers to meet high demand without compromising quality.
Advanced Die Design: Innovations in die technology have led to improved flow characteristics and reduced material waste during production. This results in more efficient use of raw materials and lower production costs.
Energy-Efficient Equipment: Newer extruders are designed to consume less energy while maintaining high output levels. This not only reduces operational costs but also aligns with global sustainability goals by minimizing environmental impact.
Benefits of Enhanced Extrusion Techniques
The advancements in glass door seal strip extrusion translate into numerous benefits for manufacturers and end-users alike:
Improved Product Quality: Enhanced precision in the extrusion process ensures that each seal strip meets exact specifications, reducing defects and improving overall performance.
Customization Options: With advanced extrusion techniques, manufacturers can easily customize seal strips for specific applications or customer requirements, providing tailored solutions that meet diverse needs.
Cost Savings: The combination of reduced material waste, lower energy consumption, and increased production speeds contributes to significant cost savings throughout the manufacturing process.
Sustainability: By optimizing material usage and energy consumption, modern extrusion methods support sustainable manufacturing practices that are increasingly important to consumers and regulatory bodies alike.
Broader Application Range: Innovations in extrusion technology allow for the production of seal strips suitable for various environments—whether residential, commercial, or industrial—enhancing their versatility across multiple sectors.
Future Trends in Seal Strip Extrusion
Looking ahead, several trends are likely to shape the future of glass door seal strip extrusion:
Smart Materials: The integration of smart materials that respond to environmental changes (e.g., temperature fluctuations) could enhance sealing performance further.
Recyclable Materials: As sustainability becomes a priority, there will be a push towards using recyclable materials in seal strip production without compromising quality or performance.
Digital Manufacturing: The adoption of digital technologies such as 3D printing may allow for even greater customization options and rapid prototyping capabilities in seal strip design.
Enhanced Testing Methods: Advances in testing technologies will enable manufacturers to better assess the performance of seal strips under various conditions before they reach consumers.
Conclusion
Innovations in glass door seal strip extrusion are transforming how manufacturers produce these critical components. By enhancing efficiency and quality through advanced technologies such as co-extrusion, automation, and energy-efficient equipment, manufacturers can meet growing market demands while adhering to sustainability goals. As these trends continue to evolve, we can expect even more significant advancements that will further improve product performance and environmental impact. The future of glass door seal strips looks promising as technology continues to drive innovation in this essential sector.