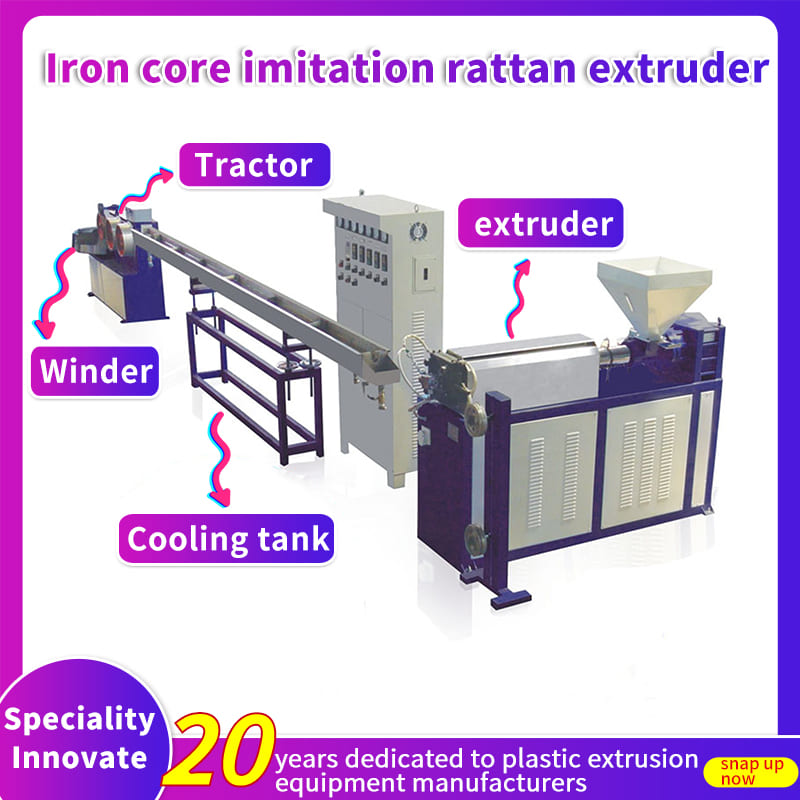
How to Choose the Right Plastic Rattan Extruder?
Choosing the right plastic rattan extruder is a critical decision for manufacturers looking to produce high-quality synthetic rattan products. With a multitude of options available in the market, understanding the key factors that influence the selection process is essential for ensuring optimal production efficiency, product quality, and cost-effectiveness. This article will guide you through the considerations to keep in mind when selecting a plastic rattan extruder, helping you make an informed decision that aligns with your business goals.
Understanding Plastic Rattan Extruders
Plastic rattan extruders are specialized machines designed to produce synthetic rattan materials from various polymer resins such as polyethylene (PE), polypropylene (PP), and polyvinyl chloride (PVC). The extrusion process involves melting these materials and forcing them through a die to create long strips that resemble natural rattan. These strips are then used in various applications, including furniture, decorative items, and outdoor structures.
Key Features of Plastic Rattan Extruders
When evaluating different plastic rattan extruders, consider the following key features:
Screw Design: The screw is a crucial component of the extruder that affects productivity, plasticizing quality, and the overall efficiency of the machine. A well-designed screw can ensure better mixing and melting of materials, leading to higher-quality output.
Temperature Control: Maintaining precise temperature control during the extrusion process is vital for achieving consistent product quality. Look for machines with advanced temperature control systems that can adapt to different materials and production conditions.
Production Capacity: Assess your production requirements and choose an extruder that can handle your desired output volume. Machines with higher production capacities can help meet increasing demand while maintaining efficiency.
Material Compatibility: Ensure that the extruder can process the types of polymers you plan to use. Some machines are designed to work with multiple materials, allowing for greater flexibility in production.
Energy Efficiency: Energy-efficient machines can significantly reduce operational costs. Look for models equipped with energy-saving technologies that optimize power consumption without sacrificing performance.
User-Friendly Interface: An intuitive control panel and automated settings can simplify operations and reduce the learning curve for operators. This feature is particularly important for businesses with less experienced staff.
Factors to Consider When Choosing a Plastic Rattan Extruder
1. Production Requirements
Before selecting an extruder, assess your specific production needs. Consider factors such as:
Output Capacity: Determine how much synthetic rattan you need to produce daily or weekly. Choose a machine that can meet or exceed these requirements.
Product Specifications: Identify the types of rattan products you plan to manufacture (e.g., round rattan, flat rattan) and ensure the extruder can produce these specifications.
2. Machine Type
Different types of plastic extrusion processes require specific machine configurations:
Single-Screw Extruders: Suitable for producing simple profiles and have lower maintenance costs.
Twin-Screw Extruders: Ideal for processing more complex materials and achieving better mixing capabilities but may come at a higher cost.
Choose the type that best fits your production needs and budget constraints.
3. Quality and Reliability
Investing in a high-quality machine is crucial for long-term success. Research potential manufacturers by checking customer reviews, industry reputation, and certifications. Reliable machines reduce downtime and maintenance costs, ensuring consistent production flow.
4. Technical Support and After-Sales Service
Opt for suppliers that offer robust after-sales support, including training, maintenance services, and readily available spare parts. Prompt assistance during technical issues can minimize downtime and keep your production running smoothly.
5. Cost vs. Value
While price is an important consideration, focus on the overall return on investment (ROI) rather than just upfront costs. Evaluate factors such as machine performance, durability, maintenance requirements, and potential for future upgrades to determine its long-term value for your business.
6. Safety Features
Safety should always be a priority in manufacturing environments. Look for machines that come equipped with safety features such as emergency stop buttons, protective guards, and compliance with industry safety standards.
Conclusion
Selecting the right plastic rattan extruder is a multifaceted decision that requires careful consideration of various factors. By thoroughly evaluating these considerations, you can make an informed decision that aligns with your business goals while enhancing productivity and maximizing return on investment.
Investing in a high-quality plastic rattan extruder not only improves operational efficiency but also positions your business competitively in the market by enabling you to produce high-quality synthetic rattan products tailored to customer preferences.