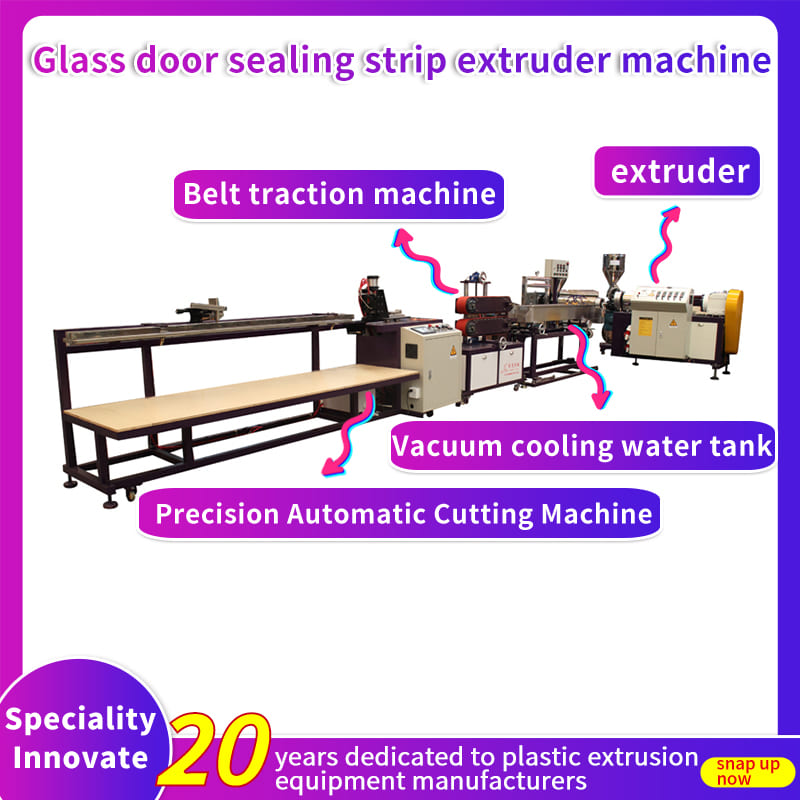
How to Choose the Right Extruder for Window and Door Seal Strips?
Window and door seal strips are crucial for energy efficiency, weatherproofing, and sound insulation in buildings. Manufacturing these strips involves extrusion, a process that shapes materials like rubber, PVC, and TPE into continuous profiles using specialized machinery called extruders. Selecting the right extruder is vital for producing high-quality seal strips that meet specific requirements. This article provides a comprehensive guide on how to choose the right extruder for window and door seal strips, considering various factors such as material, extruder types, and application requirements.
Understanding the Extrusion Process
The extrusion process involves several key steps:
Material Selection and Preparation: Choosing the appropriate material (EPDM, Silicone, PVC, TPE) based on desired properties like weather resistance, flexibility, and cost-effectiveness. The selected material is then prepared for feeding into the extruder.
Feeding the Material: Feeding the prepared material into the extruder using a strip feeder for solid materials like rubber or a cold feeder for softer compounds.
Heating and Mixing: Heating and mixing the material inside the extruder using a rotating screw to ensure uniform temperature and pressure distribution, making it pliable for shaping.
Shaping the Profile: Forcing the heated material through a die to create the desired shape and precise cross-sectional profile for window and door seals.
Cooling and Cutting: Cooling the extruded profile in a cooling chamber to solidify it, followed by cutting it to the required length using a cutting machine.
Types of Extruders
Several types of extruders are used in the production of window and door seal strips, each suited to different materials and applications:
Single-Screw Extruders: Most common type, suitable for most thermoplastic materials. They are simple and cost-effective but may have limitations in material mixing and heat transfer.
Twin-Screw Extruders: Provide better mixing and heat transfer, making them ideal for more complex materials or coextrusion processes. They are more versatile but also more expensive.
Coextruders: Allow for the simultaneous extrusion of multiple materials, creating multi-layered seal strips with different properties in different layers, such as a sponge rubber core with a harder outer layer.
Materials Used for Seal Strips
The choice of material depends on the desired properties and application:
EPDM (Ethylene Propylene Diene Monomer): Known for excellent weather resistance and widely used for outdoor applications. It offers good UV resistance and can withstand extreme temperatures.
Features: Outstanding UV and ozone resistance, excellent elasticity and durability, withstands temperatures from -40°C to 120°C.
Silicone Rubber: Offers excellent flexibility and resistance to extreme temperatures and is often used in high-performance applications where durability is crucial.
Features: Heat resistance up to 250°C, non-toxic and safe for food-grade environments, highly flexible.
PVC (Polyvinyl Chloride): Cost-effective and easy to process, commonly used for PVC strips but may not offer the same level of weather resistance as rubber materials.
Features: Lightweight and economical, good insulation properties, moderate weather resistance.
TPE (Thermoplastic Elastomer): Combines the benefits of rubber and plastics, offering flexibility and ease of processing. TPE is used in applications where a balance between performance and cost is needed.
Nitrile Rubber Extrusions: Best for oil and fuel resistance and are perfect for garages, workshops, or areas prone to oil spills. They’re tough, durable, and ideal for heavy-duty sealing.
Features: Superior resistance to petroleum-based fluids, excellent abrasion resistance, moderate temperature range (-20°C to 100°C).
Neoprene Rubber Extrusions: Suitable for sealing both indoor and outdoor doors and windows, offering a balance of durability and flexibility.
Features: Good weather and chemical resistance, flame retardant properties, moderate elasticity.
Factors to Consider When Choosing an Extruder
Choosing the right extruder involves considering several key factors:
Material Compatibility: Ensure the extruder is compatible with the chosen material (rubber, PVC, TPE) to ensure efficient processing and quality output.
Extruder Type: Select the appropriate extruder type (single-screw, twin-screw, coextruder) based on the material complexity and desired seal strip properties. Twin-screw extruders are ideal for complex materials requiring better mixing and heat transfer. Coextruders are suitable for producing multi-layered seals.
Production Volume: Consider the required production volume to determine the extruder capacity and speed. Continuous extrusion processes offered by plastic strip machines allow for large volumes, reducing labor costs and improving production speed.
Seal Strip Dimensions and Shape: Ensure the extruder can produce seal strips with precise dimensions and shapes required for the specific application. PVC seal strip extrusion lines are designed to create strips with precise dimensions, ensuring a perfect fit for their intended applications.
Budget: Balance the cost of the extruder with its performance and durability. Cheaper options might save money upfront but could wear out faster, while more expensive options often last longer and provide better performance.
Flexibility: Determine if the extruder can handle various applications across multiple industries. PVC seal strip extrusion machines can be adapted to meet the needs of any project, whether manufacturing magnetic seal strips for doors, weatherstripping for windows, or shower door seals.
Environmental Conditions: Assess the environmental conditions the seal strips will face. For extreme weather, EPDM is a good choice, while silicone is best for high-temperature environments.
Benefits of Using High-Quality Seal Strips
Using high-quality seal strips provides several benefits:
Energy Efficiency: Seal strips reduce heat loss in winter and heat gain in summer, improving energy efficiency and reducing energy bills.
Weatherproofing: They protect against rain, dust, and drafts, ensuring interiors stay safe and sound.
Durability: Resistant to wear, UV rays, and temperature fluctuations, ensuring doors and windows are sealed for years.
Noise Reduction: Weather-stripping reduces noise from the outside when driving, enhancing comfort.
Types of Rubber Extrusions for Doors and Windows
Various types of rubber extrusions are available, each with unique features and applications:
P-Seals: Look like the letter P, with a rounded bulb and a flat stem. The bulb compresses to fill a gap and provide the sealing action, and the stem is used for attaching the gasket to a substrate.
D-Seals: Look like the letter D, with a half-moon bulb that's flat on the bottom. The bulb provides sealing under pressure, such as when an enclosure door is closed.
E-Seals: These are another common type of extruded rubber seal.
Lip Seals: These seals have a lip that creates a tight seal against a surface.
The Manufacturing Process of Rubber Extrusions
The manufacturing process of rubber extrusions involves several steps:
Select and Prepare the Rubber Compound: Different types of rubber have different properties, making them suitable for different environments and applications. The first step is to identify the most appropriate type of rubber for the product you wish to manufacture. Once you've selected your rubber, you may then blend it with additives to help achieve the desired properties.
Feed the Rubber into the Extruder: Next, the rubber should be fed into the extruder. A strip feeder is usually used for solid rubbers, whilst a cold feeder is used for softer or more sensitive compounds.
Extrusion: The rubber is then forced through a die to create the desired shape.
Shape the Product: The die is specifically designed to produce the precise cross-sectional profile required for window and door seals.
Vulcanisation: The rubber is then vulcanized to harden it.
Conclusion
Choosing the right window and door seal strip extruders requires careful consideration of material compatibility, extruder type, production volume, budget, and desired seal strip properties. By understanding the extrusion process, different types of extruders, and the properties of various materials, manufacturers can select the most suitable extruder to produce high-quality seal strips that offer enhanced durability, improved performance, and cost-effectiveness. Investing in the right extruder ensures long-term benefits, including energy efficiency, weatherproofing, and noise reduction, ultimately contributing to the comfort and sustainability of buildings.