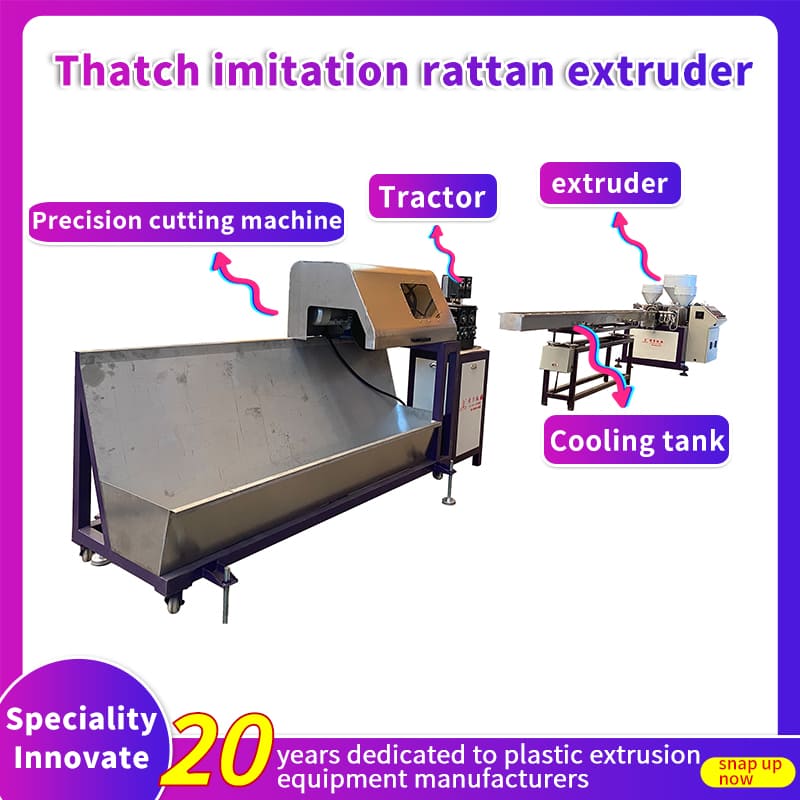
How Maximizing Efficiency with Plastic Rattan Extruders?
Maximizing efficiency in plastic rattan extrusion is essential for manufacturers looking to enhance productivity, reduce costs, and maintain high-quality output. As the demand for synthetic rattan products continues to grow, optimizing the extrusion process becomes increasingly important. This article will explore various strategies and best practices to maximize efficiency with plastic rattan extruders, covering aspects such as equipment selection, process optimization, and energy management.
Understanding Plastic Rattan Extrusion
Plastic rattan extrusion involves melting polymer resins such as polyethylene (PE) or polypropylene (PP) and shaping them into long strands that resemble natural rattan. These strands are then used in various applications, particularly in furniture manufacturing. Several factors, including the design of the extruder, the quality of raw materials, and the operational parameters influence the efficiency of this process.
Key Components of an Efficient Extrusion Process
Extruder Design: The design of the extruder plays a crucial role in determining its efficiency. A well-designed screw and barrel can significantly enhance the melting and mixing of materials, leading to better product quality and reduced energy consumption.
Temperature Control: Maintaining precise temperature control throughout the extrusion process is vital for achieving consistent results. Overheating can lead to material degradation, while insufficient heating can result in poor flow characteristics.
Material Quality: The quality of the raw materials used in the extrusion process directly impacts efficiency. High-quality resins with consistent properties will yield better results compared to lower-quality alternatives.
Process Parameters: Optimizing parameters such as screw speed, feed rate, and cooling times can greatly influence production efficiency. Each parameter must be carefully calibrated to achieve the desired output while minimizing waste.
Strategies for Maximizing Efficiency
1. Selecting the Right Equipment
Choosing the right plastic rattan extruder is fundamental to maximizing efficiency. Consider the following factors when selecting equipment:
Screw Design: The screw design should be tailored to the specific type of polymer being processed. A well-designed screw can improve material melting and mixing, reducing energy consumption by up to 50% when running at optimal speeds.
Production Capacity: Ensure that the extruder can handle your production requirements without frequent downtime. High-capacity machines are designed for continuous operation, which is essential for meeting high demand.
Energy Efficiency Features: Look for extruders equipped with energy-saving technologies that optimize power consumption during operation. These features can significantly reduce operational costs over time.
2. Process Optimization
Optimizing the extrusion process involves fine-tuning various parameters to enhance overall performance:
Temperature Management: Implement advanced temperature control systems that ensure uniform heating throughout the barrel and die. This consistency helps maintain product quality while reducing energy waste.
Screw Speed Adjustment: Running the extruder at its maximum design speed typically results in greater energy efficiency. Adjusting screw speed based on material characteristics can also help achieve optimal melting rates.
Feed Rate Control: Maintaining a consistent feed rate ensures smooth operation and prevents interruptions in production. Automated feeding systems can help regulate material input effectively.
3. Energy Management
Energy consumption is a significant factor in extrusion operations. Implementing strategies to manage energy use can lead to substantial cost savings:
Minimize Barrel Cooling: Excessive barrel cooling can indicate inefficiencies in screw design or operation. By optimizing screw geometry and minimizing unnecessary cooling, manufacturers can reduce energy consumption significantly.
Preheating Materials: Preheating resin pellets before they enter the extruder can enhance melting capacity and reduce energy requirements during extrusion.
Regular Maintenance: Keeping equipment well-maintained ensures that it operates at peak efficiency. Regular inspections and timely repairs prevent breakdowns that could lead to increased energy use and production delays.
4. Training and Workforce Development
A skilled workforce is essential for maximizing efficiency in plastic rattan extrusion:
Operator Training: Providing comprehensive training for operators on machine operation, maintenance, and troubleshooting can enhance overall productivity. Skilled operators are better equipped to identify issues early and make necessary adjustments.
Continuous Improvement Programs: Implementing programs that encourage feedback from operators can lead to ongoing improvements in processes and practices.
Conclusion
Maximizing efficiency with plastic rattan extruders is a multifaceted endeavor that requires careful consideration of equipment selection, process optimization, energy management, and workforce training. By focusing on these areas, manufacturers can enhance productivity while maintaining high-quality output and reducing operational costs.
Investing in advanced technology, optimizing production parameters, and fostering a skilled workforce will position manufacturers to meet growing market demands effectively. As competition increases within the industry, those who prioritize efficiency will not only improve their bottom line but also contribute positively to sustainability efforts by minimizing waste and energy consumption.
In summary, adopting a holistic approach toward maximizing efficiency in plastic rattan extrusion will yield significant benefits for manufacturers looking to thrive in today's dynamic market landscape.