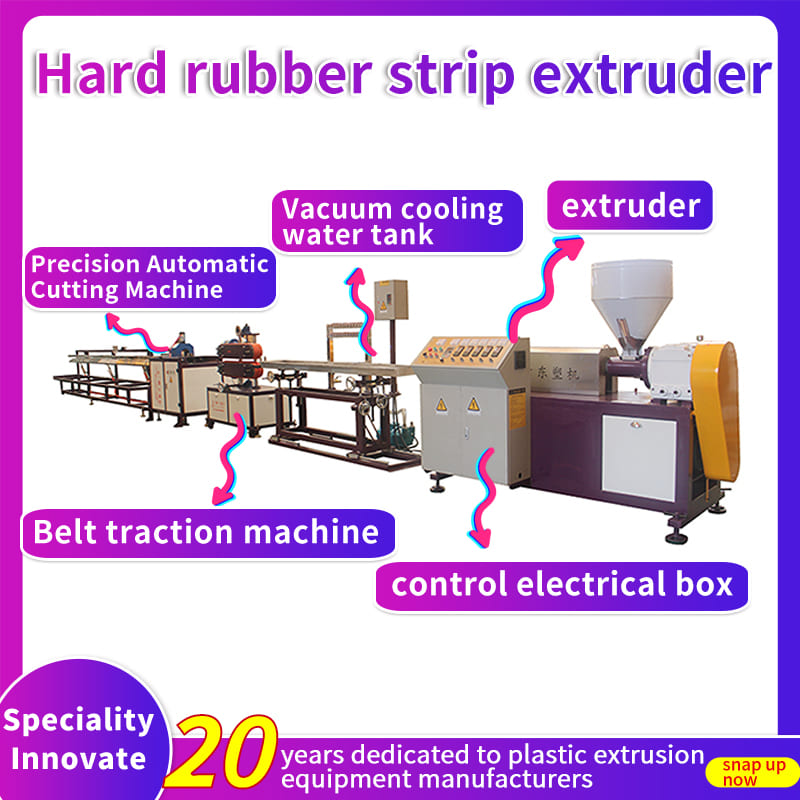
High-Speed Strip Extrusion: Revolutionizing Production Efficiency
High-speed strip extrusion is transforming manufacturing, offering unprecedented levels of production efficiency and opening doors to new possibilities across various industries. This advanced manufacturing process leverages cutting-edge technology to produce high-quality strips at remarkable speeds, reducing production time, minimizing material waste, and ultimately revolutionizing how products are made.
Understanding High-Speed Strip Extrusion
Extrusion, in general, is a manufacturing process where the material is pushed through a die of the desired cross-section. This process is commonly used with materials like plastics and aluminum to create a variety of shapes and profiles. High-speed strip extrusion takes this concept to the next level by optimizing the process for speed and efficiency. This involves advancements in machinery, die design, and process control to achieve significantly higher output rates compared to traditional extrusion methods.
The Mechanics of High-Speed Strip Extrusion
The high-speed strip extrusion process involves several key steps:
Material Preparation: The raw material, typically in the form of granules or powder, is fed into the extruder. For plastics, this often involves a blend of polymers and additives to achieve specific properties such as flexibility, rigidity, or color.
Melting and Homogenization: The material is then heated and melted inside the extruder. Screws within the extruder ensure the material is thoroughly mixed and homogenized, ensuring consistent quality. Single screw and twin screw extrusion machines are commonly used, with twin screw extruders being preferred when special colors or attributes are needed.
Extrusion Through the Die: The molten material is forced through a specially designed die that determines the shape and dimensions of the strip. The die is a flat disk of metal, typically made of hardened tool steel, with the desired profile cut into it.
Cooling and Solidification: As the strip exits the die, it is cooled to solidify the material and maintain its shape. This can be achieved through air cooling or water quenching.
Cutting and Winding: Finally, the continuous strip is cut into desired lengths or wound onto a spool for further processing or shipment. Shearing machines with automated blades cut the extrusion to a manageable length as it exits the die.
Revolutionizing Production Efficiency
High-speed strip extrusion revolutionizes production efficiency in several ways:
Increased Output: High-speed extrusion lines can produce strips at rates significantly faster than traditional methods.
Reduced Production Time: The increased output directly translates to reduced production time, allowing manufacturers to fulfill orders faster and meet market demands more effectively.
Lower Labor Costs: The automated nature of high-speed extrusion reduces the need for manual labor, lowering labor costs and minimizing the risk of human error.
Minimized Material Waste: The precision of the extrusion process minimizes material waste, leading to a more sustainable and cost-effective production process.
Energy Efficiency: Some high-speed extrusion processes are designed to be energy-efficient, consuming less energy per unit of output compared to traditional methods. High-speed extrusion consumes up to 15% less energy per revolution and saves production space because one high-speed extrusion line can finish the job of several traditional extrusion lines in the same amount of time.
Applications Across Industries
High-speed strip extrusion finds applications in a wide range of industries, including:
Medical: High-speed extrusion is used to produce medical-grade tubing for various applications, such as inserter tubing, infusion cannula, and catheter shafts. The cleanroom environment in some high-speed extrusion facilities ensures the tubing meets the stringent requirements for medical applications.
Packaging: High-speed extruders are used for processing polypropylene (PP) and high-impact polystyrene (HIPS) in the packaging industry. These extruders can produce structures at high rates and are often close-coupled to other machinery for efficient production.
Pharmaceutical: High-speed strip packing machines are used to pack tablets, pills, and capsules in strips for the pharmaceutical industry. These machines are designed with advanced technology to fulfill the mandatory requirements of the industry and can operate at high speeds.
Construction: Plastic strips produced by extrusion are used in various construction applications, such as curtain tracks, door frames, door trims, and window seals. Aluminum extrusion is also used for applications requiring light and durable components such as railings, corrugated panels, or tubes.
Automotive: PVC sealing strips are used in the automotive industry for soundproofing and insulation. These strips are designed to meet the exact standards required for different vehicles and can be produced efficiently using PVC sealing strip extrusion machines.
Advantages of Alternative Methods
Compared to other manufacturing methods like rolling, high-speed strip extrusion offers several advantages:
Complex Geometries: Extrusion is particularly useful for manufacturing components with complex geometries, such as custom profiles or hollow sections. Extrusion can create complex cross sections that might otherwise be difficult with other methods.
Customization: Extrusion allows for highly customized designs, with the ability to add features like grooves, holes, or flanges.
Uniform Material Properties: The extrusion process ensures uniform material properties throughout the length of the profile, which is critical in applications where tighter tolerances are required.
Cost-Effectiveness: Extrusion is a cost-effective solution for high-volume production due to its ability to produce profiles continuously with reduced material wastage.
Challenges and Considerations
While high-speed strip extrusion offers numerous benefits, there are also challenges and considerations to keep in mind:
Die Design: Designing and manufacturing dies for high-speed extrusion requires expertise and precision. The dies must maintain their complex shape even under high-pressure conditions.
Material Selection: Choosing the right material for the extrusion process is crucial to achieving the desired properties and performance.
Process Control: Maintaining precise control over temperature, pressure, and speed is essential for ensuring consistent quality and preventing defects.
Conclusion
High-speed strip extrusion is revolutionizing production efficiency across various industries. Its ability to produce high-quality strips at remarkable speeds, reduce production time, minimize material waste, and lower costs makes it an attractive alternative to traditional manufacturing methods. As technology continues to advance, high-speed strip extrusion will play an increasingly important role in shaping the future of manufacturing.