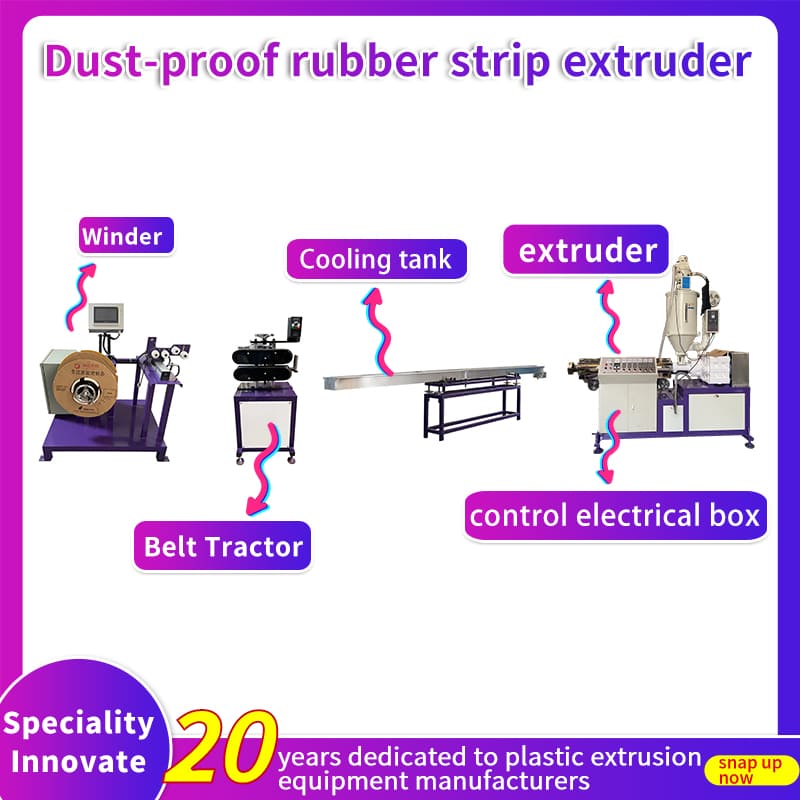
A Guide to Choosing the Right Dust-Proof Strip Extruder for Your Business Needs
In the modern manufacturing landscape, maintaining a clean and efficient production environment is crucial for businesses seeking to enhance product quality and reduce operational costs. One key component in achieving this goal is the use of dust-proof strip extruders, which play a vital role in preventing dust and other contaminants from entering production lines. This guide is designed to help businesses navigate the process of selecting the right dust-proof strip extruder tailored to their specific needs.
Introduction to Dust-Proof Strip Extruders
Dust-proof strip extruders are specialized machines used in various industries, including automotive, construction, and manufacturing, to produce flexible or rigid strips that serve as seals or barriers against dust, water, and other environmental factors. These strips are essential for maintaining product integrity and ensuring that machinery operates smoothly without the interference of unwanted particles.
Benefits of Dust-Proof Strip Extruders
Efficiency and Cost Savings: Dust-proof strip extruders are designed to reduce labor costs by automating processes such as weighing, meter counting, winding, cutting, and punching. This automation not only saves time but also minimizes the risk of human error, leading to higher quality products.
Environmental Sustainability: By reducing dust and other contaminants, these extruders contribute to a cleaner production environment. This is particularly important in industries where dust can pose health risks or compromise product quality.
Versatility: Dust-proof strip extruders can produce a variety of strip types, including flexible, rigid, or combinations of both, catering to different applications and industries.
Key Considerations When Choosing a Dust-Proof Strip Extruder
1. Business Needs and Applications
Before selecting a dust-proof strip extruder, it's essential to understand the specific needs of your business. Consider the types of strips you need to produce, the materials required, and the intended applications. For instance, if your business focuses on automotive seals, you may require strips that are resistant to extreme temperatures and chemicals.
2. Machine Specifications
Output Capacity: Determine the volume of strips you need to produce per hour. Machines like the SJ80 and SJ90 offer higher outputs, making them suitable for large-scale operations.
Power Requirements: Consider the driving power and heating power needed for your production process. Higher power machines can handle more complex materials and larger outputs.
Heating Zones: More heating zones allow for better temperature control, which is crucial for producing consistent quality strips.
3. Material Selection
The choice of materials for the strips depends on their intended use. For example, EPDM rubber is commonly used for outdoor applications due to its resistance to UV rays and ozone, while silicone rubber is preferred for high-temperature environments.
4. Automation Features
Look for machines with advanced automation features such as automatic cutting and punching. These features not only reduce labor costs but also enhance precision and consistency in strip production.
5. Maintenance and Support
Consider the maintenance requirements of the machine and the level of support provided by the manufacturer. Regular maintenance can extend the lifespan of the extruder and prevent downtime.
Industry Applications of Dust-Proof Strip Extruders
Dust-proof strip extruders are versatile and find applications across various industries:
Automotive Industry: Used for car door seals, windshield seals, and trunk seals to prevent dust and water entry.
Construction Industry: Essential for sealing doors and windows in buildings, enhancing energy efficiency by reducing air leaks.
Manufacturing Industry: Used to seal machinery parts and prevent dust entry, ensuring smooth operation and reducing maintenance needs.
Case Studies: Successful Implementation of Dust-Proof Strip Extruders
Automotive Manufacturing: A leading automotive parts supplier implemented dust-proof strip extruders to improve the quality of their door seals. This resulted in a significant reduction in customer complaints related to dust entry and improved overall product reliability.
Construction Materials: A construction materials company used dust-proof strip extruders to produce weatherstripping for windows and doors. This helped reduce air leaks, improving energy efficiency in buildings and enhancing customer satisfaction.
Best Practices for Optimizing Dust-Proof Strip Extruder Performance
Regular Maintenance: Ensure that all moving parts are well-lubricated and filters are cleaned regularly to maintain optimal performance.
Training Personnel: Provide comprehensive training to operators to ensure they understand the machine's capabilities and limitations.
Quality Control: Implement rigorous quality control measures to ensure that strips meet the required standards for thickness, flexibility, and material composition.
Conclusion
Choosing the right dust-proof strip extruder is a critical decision for businesses seeking to enhance their manufacturing processes. By understanding the specific needs of your business, considering key machine specifications, and evaluating industry applications, you can select an extruder that not only meets but exceeds your expectations. Whether you are in the automotive, construction, or manufacturing sector, investing in a high-quality dust-proof strip extruder can lead to improved product quality, reduced operational costs, and a cleaner, more efficient production environment.