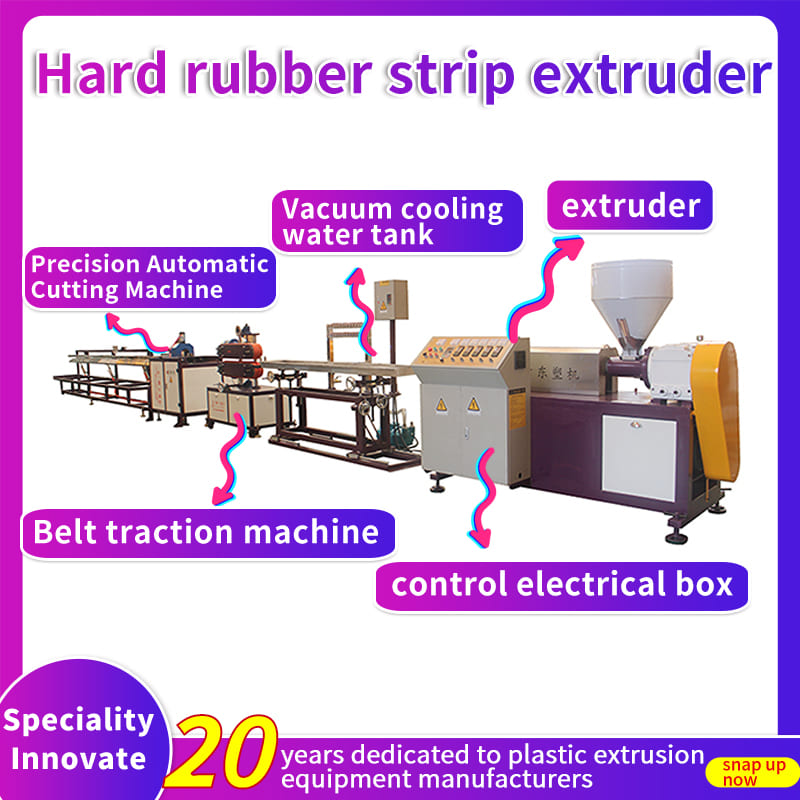
5 Essential Features of Heavy-Duty Rubber Strip Extruders
Heavy-duty rubber strip extruders are crucial in the manufacturing of robust and durable rubber products, such as seals, gaskets, and profiles used in various industrial applications. These extruders are designed to handle high-pressure and high-temperature conditions, ensuring the production of quality rubber strips that meet stringent industrial standards. In this article, we will delve into the five essential features of heavy-duty rubber strip extruders, highlighting their significance in enhancing productivity, efficiency, and product quality.
1. Robust Design and Construction
Heavy-duty rubber strip extruders are built with robust materials and designs to withstand the rigors of continuous operation under high pressure and temperature conditions. These machines typically feature stainless steel or hardened steel components for durability and resistance to corrosion. The robust construction ensures that the extruder can maintain its structural integrity even when processing dense rubber compounds, thereby reducing maintenance downtime and extending the lifespan of the machine.
For instance, RMS rubber extruders are known for their rugged design, which includes replaceable hardened liners in the barrels. This feature not only enhances durability but also simplifies maintenance by allowing easy replacement of worn-out parts. Such robust designs are essential for maintaining consistent production quality and minimizing operational costs.
2. Advanced Cooling Systems
Cooling systems play a vital role in the rubber extrusion process. They are responsible for cooling the extruded rubber to stabilize its structure and prevent deformation. This step is crucial for maintaining product quality and ensuring proper bending and flexibility without compromising durability. Heavy-duty rubber strip extruders often incorporate sophisticated cooling systems that can efficiently manage the temperature of the extrudate, ensuring that it cools uniformly and quickly.
Advanced cooling systems may include water cooling or air cooling mechanisms, depending on the specific requirements of the extrusion process. These systems help in achieving precise control over the cooling rate, which is essential for producing rubber strips with consistent dimensions and properties. Efficient cooling also helps in reducing the time required for the extrudate to reach a stable state, thereby increasing production throughput.
3. High-Performance Drive Systems
The drive system of a heavy-duty rubber strip extruder consists of a powerful motor and efficient power transmission units. This system is designed to provide consistent and reliable power to the extruder's screw, ensuring that the rubber material is processed uniformly and efficiently. High-performance drive systems enable the extruder to handle a wide range of rubber compounds, from soft and flexible materials to dense and hard ones.
For example, RMS extruders come equipped with drive motors ranging from 10 HP to 125 HP, depending on the model and application. This flexibility in motor size allows manufacturers to tailor the extruder's power output to specific production needs, optimizing energy consumption while maintaining high productivity levels.
4. Precision Dies and Tooling
The die is a critical component of any rubber extruder as it determines the cross-sectional shape and size of the extruded rubber strip. Heavy-duty rubber strip extruders often feature precision-engineered dies that are designed to produce strips with tight tolerances and uniform dimensions. These dies are typically made from high-quality steel alloys to ensure durability and resistance to wear.
Precision dies allow for the production of complex profiles, such as dual hardness extrusions, which combine different materials or hardness levels in a single extrusion. This capability is particularly useful in applications where both durability and enhanced sealing properties are required. The use of precision dies also facilitates the creation of custom profiles tailored to specific industrial needs, making heavy-duty rubber strip extruders versatile tools in various manufacturing settings.
5. Efficient Material Handling and Feeding Systems
Efficient material handling and feeding systems are essential for maintaining a smooth and continuous extrusion process. Heavy-duty rubber strip extruders often incorporate advanced feeding systems, such as high-intake hoppers and leak-free feed roll arrangements, to ensure a consistent and reliable material supply.
These systems help in minimizing material losses and reduce the risk of contamination, which can compromise product quality. For instance, RMS extruders feature a specially designed high-intake hopper that provides improved feeding, ensuring that the rubber material is fed into the extruder uniformly and consistently. This not only enhances productivity but also contributes to cost savings by reducing waste and minimizing downtime due to material-related issues.
Conclusion
Heavy-duty rubber strip extruders are indispensable in the production of high-quality rubber strips used in demanding industrial applications. The five essential features discussed—robust design, advanced cooling systems, high-performance drive systems, precision dies, and efficient material handling—collectively contribute to the efficiency, productivity, and reliability of these machines. By understanding and leveraging these features, manufacturers can optimize their production processes, ensuring the consistent delivery of durable and versatile rubber products that meet the stringent requirements of various industries.
In conclusion, investing in heavy-duty rubber strip extruders with these essential features can significantly enhance manufacturing capabilities, leading to improved product quality, reduced operational costs, and increased competitiveness in the market. As technology continues to evolve, the development of more advanced extruders will further expand the possibilities for rubber product manufacturing, enabling the creation of innovative solutions for emerging industrial challenges.